Download White Paper
Triton Edge: The Promise Of Industrial Embedded Vision Systems
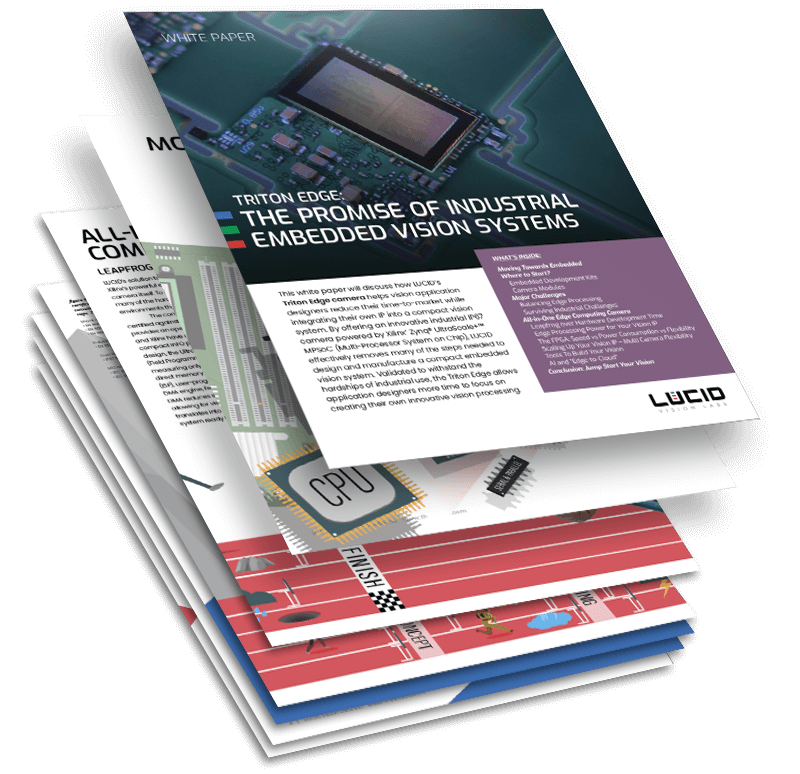
Learn how LUCID’s Triton Edge camera helps vision application designers reduce their time-to-market while integrating their own IP into a compact vision system. By offering an innovative industrial IP67 camera powered by Xilinx®’ Zynq® UltraScale+™ MPSoC (Multi-Processor System-on-Chip), LUCID effectively removes many of the steps needed to design and manufacture a compact embedded vision system. Validated to withstand the hardships of industrial use, the Triton Edge allows application designers more time to focus on creating their own innovative vision processing.
What’s Inside:
Moving Towards Embedded
Where to Start?
• Embedded Development Kits
• Camera Modules
Major Challenges
• Balancing Edge Processing
• Surviving Industrial Challenges
All-in-One Edge Computing Camera
• Leapfrog over Hardware Development Time
• Edge Processing Power for Your Vision IP
• The FPGA: Speed vs Power Consumption vs Flexibility
• Scaling Up Your Vision IP – Multi Camera Flexibility
• Tools To Build Your Vision
• AI and “Edge-to-Cloud”
Conclusion: Jump Start Your Vision
Sneak Peek
utilizing both the camera’s on-board image processing and by adding unique vision
processing to run on the embedded development board. Compared to a modern Intel/AMD PC, development boards are more limited in resources and application designers need to strategically balance available resources between components. If a balance can be found and a proof-of-concept (POC) is viable, the POC can be prototyped into more portable applications such as kiosks, aerial drones, and autonomous robotics where it is beneficial for edge processing (localized processing that happens on the embedded vision system instead of the host PC, server, or cloud.) This is also true in the industrial space, where vision systems using embedded hardware technologies are benefiting from streamlined designs that offer custom image processing such as AI inference for object detection and classification, along with a smaller physical footprint and reduced power consumption.