CASE STUDY
Industry: Lumber/Wood Processing
Product: Triton 5 MP camera
SDK: Custom software
Automated Wood Surface Inspection Using Machine Vision Cameras
Wood inspection can be challenging because all wooden materials are unique in their characteristics and classification. A high-quality inspection is key to detecting imperfections—including knots, splits, and cracks that occur during the manufacturing of wood paneling and boards—and to preventing costly returns and waste. While automated grading machines can capture true deficiencies in wood, they may miss markings due to misaligned knives or other manufacturing complications. Proper illumination is also important because surface finish defects in wood are otherwise difficult to spot.
With these challenges in mind, it’s crucial to assist and augment a human inspector’s job with a vision system that can capture images of wood surfaces in the correct illumination and freeze frame the boards. This allows the inspector to zoom in and see the board up close so they can correctly diagnose the problem directly from the machinery and prevent any issues from replicating with other boards.
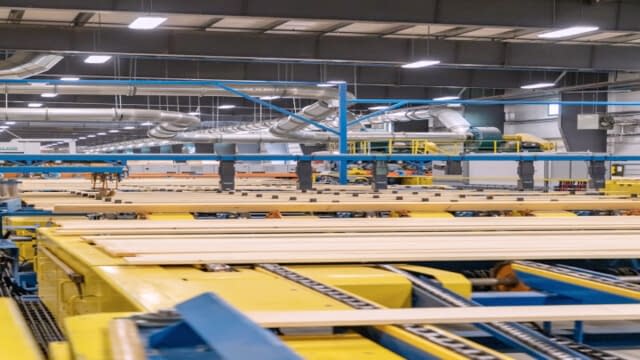
A high-quality inspection process avoids costly returns and waste and is necessary to detect imperfections in wood, including knots, splits, and cracks that can occur during the manufacturing process.
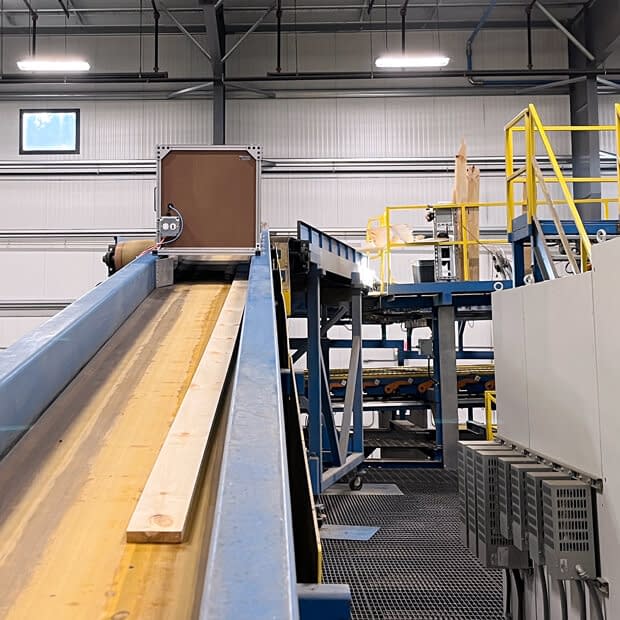
Challenge
Durgin and Crowell Lumber Company specializes in manufacturing interior paneling and exterior siding from kiln-dried Eastern white pine. Inspecting the wooden boards before they leave the facility is important because consumers don’t want unsightly streaks or indentations on the walls, ceilings, or floors of their homes. Throughout its history, the sawmill has employed people to grade and inspect the boards. Given the tight labor market and other challenges that have impacted their operations, they decided to enhance their quality control team by adding a remote element to illuminate and accelerate the inspection process. While the automated grader efficiently categorizes boards into grades, it does not catch manufacturing imperfections. Therefore, the mill added an inspection system that would catch manufacturing defects so the inspectors can make timely and calculated decisions after the boards go through the moulders.
Solution
Bodkin Design & Engineering specializes in imaging solutions and was tasked with creating a high-speed machine vision system to find hard-to-see defects and imperfections on the surface of the boards caused by the manufacturing process. The vision solution, called the Surface Finish Inspector, allows the mill’s quality control staff to view the boards on computer monitors located in the control room, on the plant floor, or even remotely from other locations.
The Surface Finish Inspector is housed in a 2-by-1.5-by-6-foot enclosure that prevents uncontrolled ambient light from interfering with the imaging process. Images are taken as the boards move through the enclosure via a conveyor system.
The vision system uses LUCID’s Triton cameras featuring 5 MP Sony Pregius IMX264 sensors. Bodkin Engineers set the frame rate by the board’s speed and field of view so that the images can be concatenated together without gaps. They also set pixel field of view and blur spot by the mill’s desired minimum detectable defect feature.
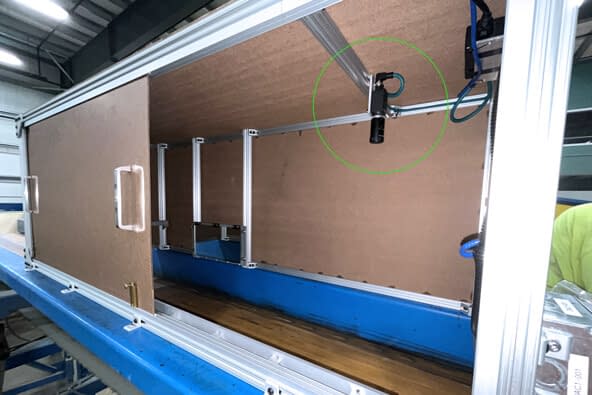
The Surface Finish Inspector allows quality control staff to view the boards on computer monitors from the control room, or even remotely.
The vision system uses LUCID’s Triton cameras featuring 5 MP Sony Pregius IMX264 sensors. Bodkin Engineers set the frame rate by the board’s speed and field of view so that the images can be concatenated together without gaps. They also set pixel field of view and blur spot by the mill’s desired minimum detectable defect feature.
Durgin and Crowell Lumber Company uses two enclosed machine vision systems: one for each of two lines where boards move along conveyors. The machine vision systems are installed immediately after the boards go through the moulder, allowing staff members the maximum amount of time to review the images in real time and decide whether they need to stop the production line to fix a problem. The moulders are installed earlier in the production process than the automated grading machine.
To enable employees to view the boards in sufficient detail, Botkin installed a structured lighting system. The machine vision system not only accentuates the defects but freeze frames the boards that are moving at 842 feet per minute. The Bodkin team designed a system with a frame rate of 21 fps with an object distance of 750 mm and a focal length of 16 mm. The image field size is 16 inches to accommodate the wood boards, which are 12 inches wide.
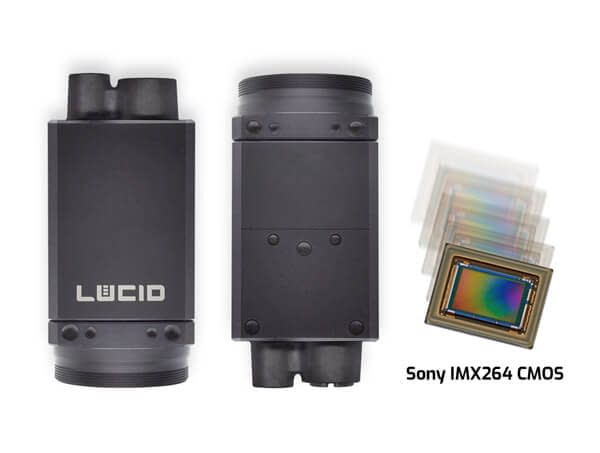
The Surface Finish Inspector uses LUCID’s Triton cameras featuring 5 MP Sony Pregius IMX264 sensors.
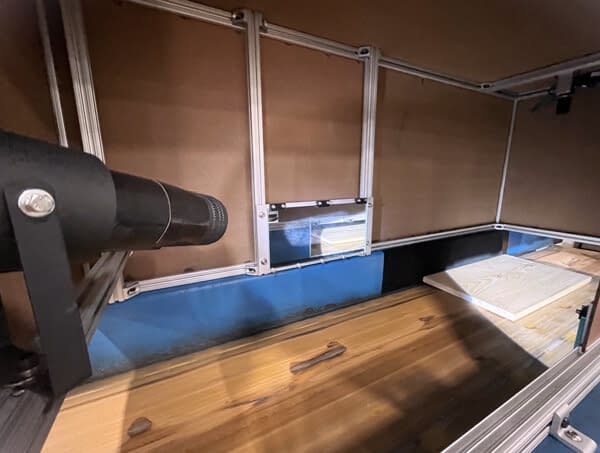
By enclosing the system, ambient light does not interfere with the imaging process.
The two imaging lines are run through a single processor setting the data rate and storage requirements for the selected computer. The image processing software, which was developed in-house, continuously concatenates all images to create one long image of the moving boards, so operators can view them continuously. Images from both systems are processed on a single PC. The sawmill accesses the Surface Finish Inspector remotely, allowing it to tweak the system as necessary, such as changing a camera’s settings, or working with the mill’s staff on modifications.
Conclusion
Automated vision systems can greatly improve inspection quality with up to 98% accuracy compared to unassisted manual labor which can capture only about 70%–80% of the defects. Hence, advanced machine vision technology can lead to a significant increase in productivity and reduction of labor costs and waste.