CASE STUDY
業界: 製材・木材加工
製品: Triton 5MPカメラ
SDK: カスタムソフトウェア
マシンビジョンカメラによる木材表面検査の自動化
木材の検査は、その特性や分類がそれぞれ異なるため、難しい作業です。高品質の検査は、木製羽目板やボードの欠陥を検出し、コストのかかる返品や無駄を防ぐための鍵となります。これには、製造工程で発生する節、割れ、ひび割れの検出も含まれます。自動グレーディング・マシンは木材の真の欠点を捉えることができますが、ナイフの位置がずれていたり、その他の製造上の問題により、マーキングを見逃すことがあります。木材の表面仕上げの欠陥は見つけにくいため、適切な照明も重要です。
このような課題を念頭に、正しい照明で木材表面の画像をキャプチャし、板をフリーズ・フレームで拡大して表示できるビジョン・システムによって、人間の検査員の作業を支援し、補強する必要がある。これにより、検査員は機械から問題を正しく診断し、他のボードで問題が再現されるのを防ぐことができる。
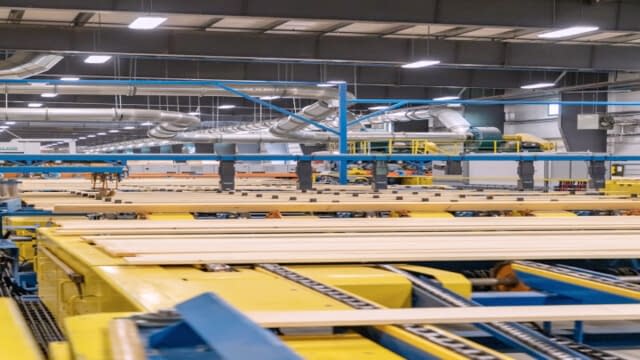
高品質の検査工程は、コストのかかる返品や無駄を省き、製造工程で発生する可能性のある節、割れ、ひび割れなどの木材の欠陥を検出するために必要である。
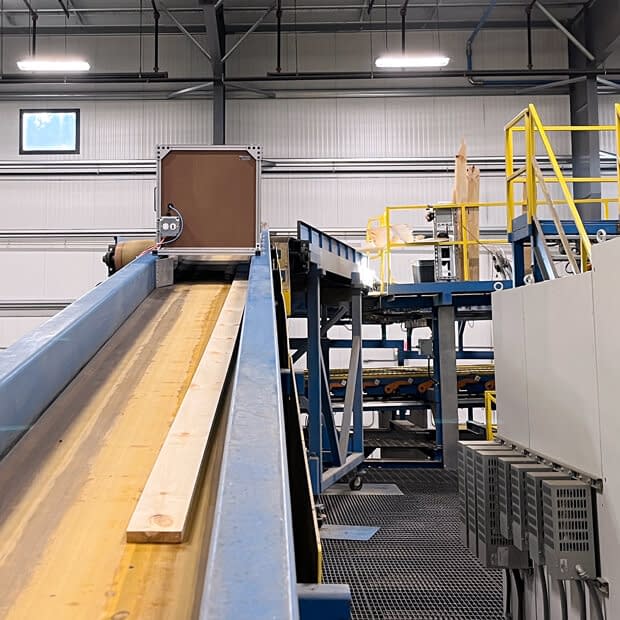
Challenge
ダージン・アンド・クロウエル製材は、イースタン・ホワイト・パイン材の内装羽目板と外装サイディングを専門としている。消費者は家の壁や天井、床に見苦しい筋や凹みをつけたくないので、施設を出る前に木の板を検査することは重要である。この製材所では、その歴史を通じて、板の等級付けと検査に人間が従事してきた。しかし、労働市場の逼迫やその他の課題が操業に影響を及ぼしたため、品質管理チームを強化するため、遠隔操作で作業を照らし、迅速化する装置を導入することにした。自動グレーダーは効率的に板を等級に分類するが、製造上の不完全な部分を捉えることはできない。そこで同工場では、ボードがモルダーを通過した後、検査員がタイムリーかつ計算された判断を下せるよう、製造上の欠陥をキャッチする検査システムを追加した。
Solution
Bodkin Design & Engineering社は画像処理ソリューションを専門としており、製造工程で発生する基板表面の見えにくい欠陥や不完全な部分を見つけるための高速マシンビジョンシステムの開発を任された。表面仕上げインスペクターと呼ばれるこの画像処理ソリューションにより、同工場の品質管理スタッフは、制御室や工場内のコンピューターモニター、あるいは他の場所から遠隔で基板を見ることができる。
表面仕上げ検査装置は、2 x 1.5 x 6フィートの筐体に収められている。システムを密閉することで、ボドキン社のエンジニアは、制御不能な環境光が画像処理プロセスの妨げにならないようにしている。画像は、基板がコンベアシステムを通って筐体内を移動する際に撮影される。
The vision system uses LUCID’s ビジョンシステムには、5MPのSony Pregius IMX264センサーを搭載したLUCIDのTritonカメラが使用されている。フレームレートは、画像が隙間なく連結されるように、基板の速度と視野によって設定された。ピクセルの視野とぼかしスポットは、希望する最小検出欠陥機能によって設定された。
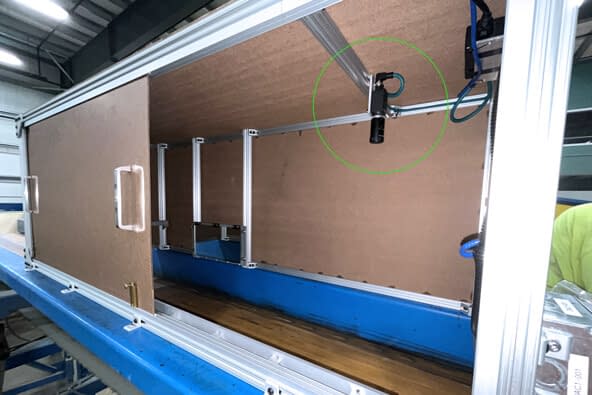
サーフェス・フィニッシュ・インスペクターは、品質管理スタッフがコントロール・ルームから、あるいは遠隔地から、コンピューター・モニターで基板を見ることができる。
このマシンビジョンシステムは、基板がコンベア上を移動する2つのラインそれぞれに1台ずつ、計2台設置されている。マシンビジョンシステムは、基板がモルダーを通過した直後に設置されているため、スタッフはリアルタイムで画像を確認し、問題を解決するために生産ラインを停止する必要があるかどうかを判断するための最大限の時間を確保できる。モルダーは、自動グレーディング・マシンよりも生産工程の早い段階で設置される。
従業員が基板を十分に詳細に見ることができるよう、構造化照明システムが採用された。マシンビジョンシステムは欠陥を際立たせるだけでなく、毎分842フィートで移動する基板をフリーズフレーム化する。ボドキンチームは、フレームレート21fps、物体距離750mm、焦点距離16mmのシステムを設計した。イメージフィールドサイズは、幅12インチの木板に対応するため16インチである。
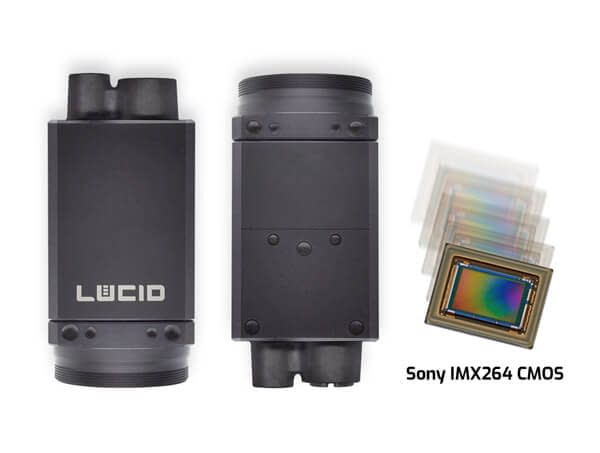
サーフェス・フィニッシュ・インスペクターは、品質管理スタッフがコントロール・ルームから、あるいは遠隔地から、コンピューター・モニターで基板を見ることができる。
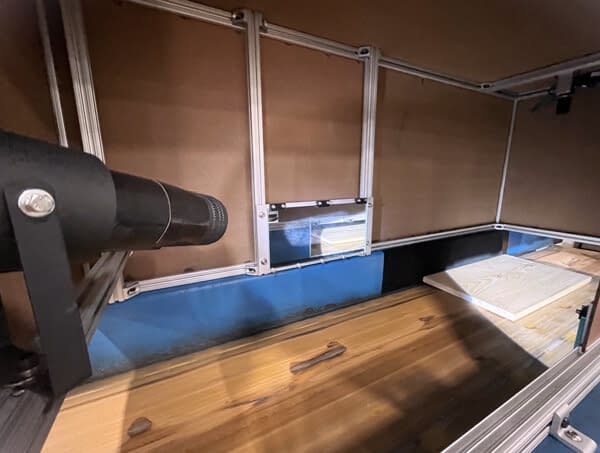
システムを密閉することで、周囲の光が画像処理に干渉しないようにしている。
2つの画像処理ラインは、選択したコンピュータのデータレートとストレージ要件を設定する1つのプロセッサを介して実行される。社内で開発された画像処理ソフトウェアは、すべての画像を連続的に連結して、動いているボードの1つの長い画像を作成し、オペレーターが連続的に見ることができるようにした。両システムの画像は、1台のPCで処理された。製材所では、遠隔操作で表面仕上げ検査システムにアクセスできるため、カメラの設定を変更するなど、必要に応じてシステムを調整したり、製材所のスタッフと協力して修正したりすることができました。
Conclusion
自動化された画像処理システムは、手作業では欠陥の約70~80%しか捉えられないのに比べ、最大98%の精度で検査品質を大幅に向上させることができる。したがって、これらの視覚的作業にマシンビジョンを使用する高度な技術は、生産性の大幅な向上、人件費と無駄の削減につながります。