CASE STUDY
Industry: Manufacturing/Packaging
Product: Triton 5.0 MP Color Camera Feat. Sony IMX264
SDK: Custom Vision Software by PENSUR Using Halcon SDK
Effizientes Vision-geführtes Pick-and-Place-System für Blisterverpackungen
Blisterverpackungen werden häufig als Einzelverpackung für Konsumgüter oder kleine Tabletten und Kapseln verwendet. Die vorgeformte Kunststoffverpackung besteht aus zwei Hauptkomponenten: einer Kavität aus Kunststoff oder Aluminium sowie einer Deckfolie aus Papier, Kunststoff, Aluminium oder einem Laminat aus weicher Folie und anderen Materialien. Die Kavität enthält das Produkt, die Deckfolie verschließt es luftdicht.
Beim Abfüllprozess werden die Produkte zunächst in die vorgeformten Kavitäten eingelegt, bevor die Deckfolie aufgebracht und versiegelt wird. Selbst wenn jedes Produkt vorab erkannt und inspiziert wurde, besteht weiterhin das Risiko von Beschädigungen oder Störungen beim Befüllen der Blister, was häufig manuelle Eingriffe erforderlich macht.

Herausforderung
Früher bestand der Sortier- und Verpackungsprozess aus zwei Schritten. Zunächst mussten die Produkte jeder Linie manuell sortiert und in Boxen verpackt werden, um sie für den nächsten Schritt griffbereit zu haben. Danach platzierte ein Bediener jede Produktbox in eine vom System geformte Blisterform. Diese manuelle Arbeit führte häufig zu arbeitsbedingten Verletzungen durch sich wiederholende Bewegungen, da täglich zehntausende Produkte verarbeitet werden. Weitere Herausforderungen waren hohe Anforderungen an Geschwindigkeit und Präzision sowie die Unterstützung unterschiedlichster Produktlinien mit verschiedenen Größen, Formen und Designs. Für eine präzise Pick-Genauigkeit von 0,5 mm musste ein spezielles Kalibrierungsverfahren entwickelt werden.
Um den manuellen Aufwand beim Sortieren und Platzieren der Boxen zu reduzieren, entwickelte Pensur, ein Ingenieurdienstleister für Automatisierungslösungen, ein effizientes Vision-basiertes Pick-and-Place-System. Schnelle, zuverlässige Hardwarekomponenten kombiniert mit optimierter und individuell angepasster Software machten die Umsetzung möglich. Spezielle Bildverarbeitungssoftware und Triton-Kameras von LUCID wurden eingesetzt, um die Produkte zuverlässig zu erkennen und zu identifizieren.
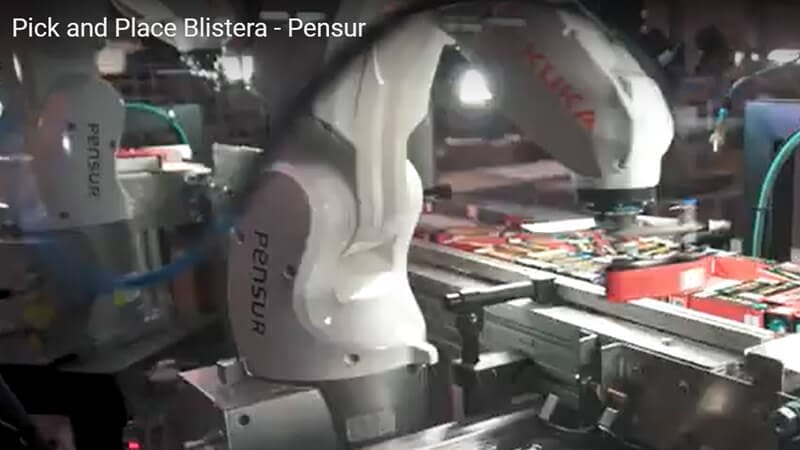
Lösung
Jedes System umfasst zwei LUCID TRI050 Farbkameras zur Lokalisierung und Identifikation der Produkte, in diesem Fall Klebeprodukte. Die GigE Vision-Kameras sind für maximale Geschwindigkeit an separate Gigabit-Ports angeschlossen und werden über optoentkoppelte Pins durch Roboter ausgelöst, um eine Synchronisierung mit dem Pick-System zu gewährleisten.
„Die Bildqualität der LUCID-Kameras in Kombination mit hochwertigen Objektiven ermöglicht eine präzise und konsistente Identifikation der Produkte über das gesamte Sichtfeld“, sagt Pablo Senatore, Elektroingenieur und Projektleiter bei Pensur. Die Softwarelösung wurde von Pensur auf Basis des Halcon SDK von MVTec entwickelt.
Das Gesamtsystem besteht aus einem Bedienpanel, einer Verarbeitungseinheit, einem Aufzugsförderband und zwei Roboter-Kamera-Förderband-Systemen. Zunächst wählt der Bediener am Steuerpult eines von über 30 Produkten aus, die verpackt werden sollen.
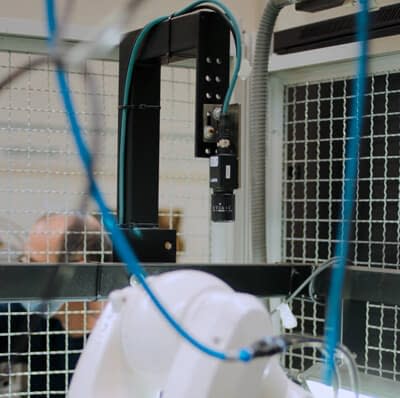
Danach gelangen die Produkte über das Aufzugsförderband zur ersten Sortierstation. Die Boxen erreichen über ein horizontales Förderband den Arbeitsbereich des ersten Roboters. Dort werden Bilder mit der LUCID Triton 5.0 MP Farbkamera aufgenommen, die mit dem Sony IMX264 Global Shutter CMOS-Sensor ausgestattet ist. Nach der Bildverarbeitung entscheidet das System, welche Box aufgenommen wird. Je nach gewünschter Ausrichtung für die Blisterstation wird die Box entsprechend auf das Förderband des zweiten Systems positioniert. Am zweiten Arbeitsplatz werden die Boxen lokalisiert, Barcodes geprüft, und anschließend vom Roboter entweder in die Blister eingelegt oder aussortiert.
Die implementierte Lösung vereint beide Schritte in einer einzigen Station. Die Produkte starten am Aufzugsförderband, wo der erste Roboter mithilfe der Triton-Kamera die Sortierung übernimmt. Diese Sortierung stellt sicher, dass die Vorderseite der Box korrekt am zweiten Roboter ankommt. In der zweiten Stufe werden die Boxen identifiziert und per Barcode verifiziert, bevor sie mit einer Taktzeit von 45 Boxen pro Minute in die Blister eingelegt werden.
Fazit
Traditionelle Pick-and-Place-Systeme für Blisterverpackungen erfordern komplexe Teach-Prozesse für jedes neue Produkt, die häufige Änderungen bei Form, Größe und Position erfordern und für Bediener schwer umzusetzen sind. Durch den Einsatz schneller und zuverlässiger Hardwarekomponenten sowie maßgeschneiderter Vision-Software bietet dieses moderne System signifikante Einsparungen, erhöht die Produktivität und Sicherheit der Mitarbeiter und sorgt für maximale Prozesseffizienz bei hoher Taktleistung.
Mehr erfahren:
Besuchen Sie Pensur
Zur Triton Produktseite